The Gas Turbine Laboratory occupies over 2,000 sq. ft. and is divided into an engine workshop area for experimental work and computational research area. Additionally, researchers have access to the ERAU super computer and all engineering laboratories on campus.
Manufacturing Facilities Available on Campus
CNC and Welding Laboratory
On-site fabrication of components for classroom design projects and student competition team deliverables is supported in the CNC and Welding Laboratory. The computer-aided manufacturing of parts is enabled by a computer numeric controlled (CNC) lathe and mill. A drill press, a cutoff saw, and welding equipment are also available in this space for student use.
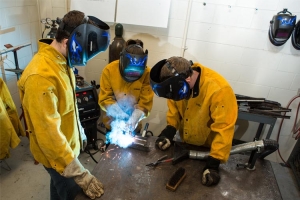
Composites Laboratory
The composites laboratory is home to graduate and faculty research projects, as well as student competition teams and collaborative undergraduate experiences in independent research, design projects, and faculty collaborations. The laboratory has a vacuum bagging system and an oven to enable the use of pre-impregnated materials that require a precise temperature for them to cure. A hot wire cutter is also available in the laboratory for the manufacture of molds.
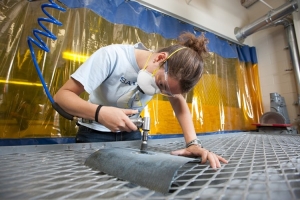
Manufacturing Laboratory
Advanced manufacturing equipment, such as Computer Numerical Control (CNC) and 3-D printing machines, are housed in the manufacturing lab alongside very basic machining tools, including lathes, mills, and routers. The lab is staffed by an experienced technician, who is in charge of supervising students, safety, and the management of this lab. Resources are provided to support undergraduate courses, student organizations, undergraduate research, and faculty research projects.
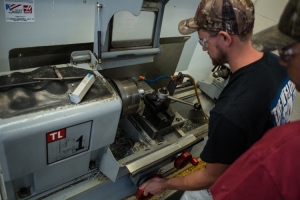
Related Research Facilities on Campus
Flight Dynamics and Control Research Laboratory
Development and implementation of guidance, navigation, and control systems for a variety of aerospace vehicles, as well as research on a broad range of topics focused on flight dynamics, are performed in the Flight Dynamics and Control Research Laboratory (FDCRL).
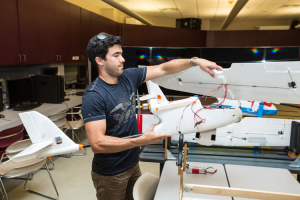
Propulsion and Aerodynamics Computational Laboratory
Numerical research in unsteady aerodynamics, acoustics, aeroelasticity, flow, and flight control are performed in the Propulsion and Aerodynamics Computational Laboratory (PACL). Computational fluid dynamics (CFD) software and industry-standard commercial codes, including CFX, Fluent, and Star-CCM+, as well as in-house research codes (including FDL3DI and BASS high-order codes for subsonic aerodynamic flows and HYP for hypersonic propulsion flows), are employed in high-fidelity simulations involving both the lab twelve dual-boot (Linux/Windows) workstations and Zeus HPC system. The equipment found in the PACL is used by undergraduate students, graduate students, research faculty, and industrial partners. Numerical studies performed here are supported by Air Force Office of Scientific Research (AFOSR), National Science Foundation (NSF), Flood Control Assistance Account Program (FCAAP), and United Launch Alliance (ULA) grants. Other research programs include unsteady aerodynamics, acoustics, aeroelasticity and flow, and flight control.
Propulsion Design Laboratory
A dedicated research laboratory for the Capstone Design Course for the Propulsion Track in Aerospace Engineering, the Propulsion Design Laboratory contains a 3D printer, conference area, and instructional area, supplemented by dedicated computers with propulsion-focused software. The overall aim of the space and the work therein is to enhance the research skills of undergraduates in line with the University’s IGNITE initiative, assist in publication for major propulsion conferences, and prepare students interested in advanced degrees (MS and/or PhD). In addition to supporting the capstone course, the lab serves the engine design competition teams that compete in the AIAA/ASME annual undergraduate engine design competition. A dedicated graduate student monitors the lab during operating hours.
Structures Laboratory
Testing is performed on the structures and components typically found in aircraft and spacecraft using the specialized equipment located in the Structures Laboratory. Standard tests performed in the laboratory include uniaxial tension/compression, bending, fatigue, vibration, ultrasonic, and acoustic emission non-destructive testing, as well as structural health monitoring. A large variety of supporting instrumentation and equipment, including shakers, accelerometers, piezoceramic transducers, storage oscilloscopes, function generators, spectrum analyzers, AC and DC standard voltage references and power supplies, power amplifiers, digital thermometers, multichannel strain gage conditioners, and digital multimeters, is available in this space.
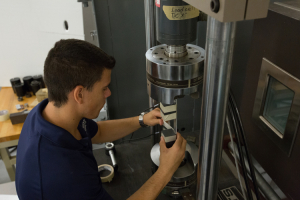
Wind Tunnel Laboratory
The primarily instructional Wind Tunnel Laboratory is used as part of the Aerospace Engineering curriculum, as well as for research by faculty and students. Located on the first floor of the Lehman Center, its main entrance is from an interior hallway; there is also access to a loading dock on the exterior of the building. This laboratory allows a series of aerodynamic experiments using the wind tunnel, manometer, and a strain gauge force balance. Experiments concerning closed duct flow include pitot-static air speed measurement and flow quality assessment. Pressure measuring experiments consist of boundary layer velocity profiles, airfoil pressure coefficients, and momentum drag. Tests using the force balance include plain and flapped wing performance and complete airplane model tests. Currently, the lab is being used solely for the above experiments. The lab has a 2-D smoke tunnel and a 3-D smoke tunnel.